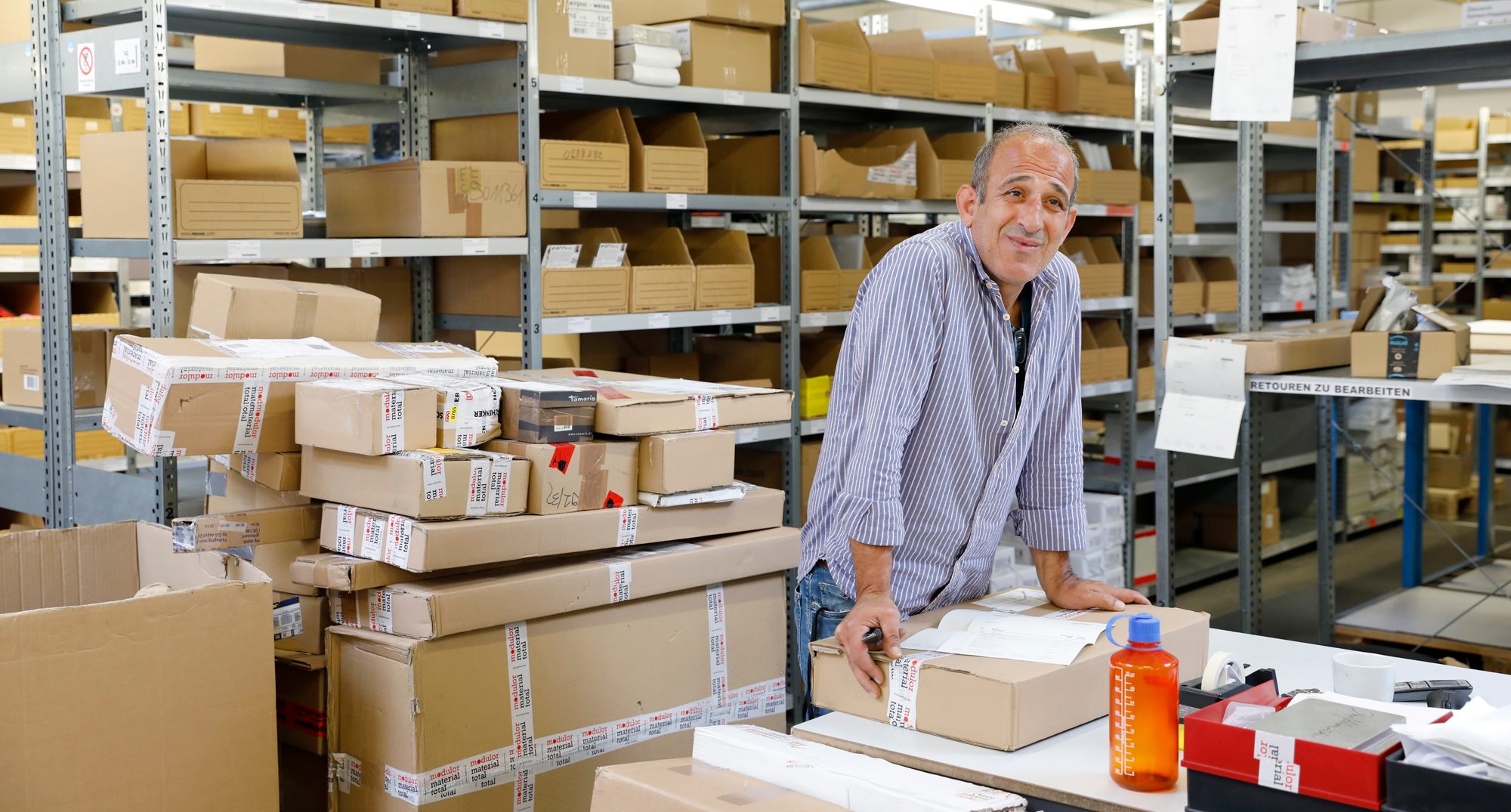
Blick hinter die Kulissen – Logistik am Moritzplatz
14:27 Uhr, knapp 13.000 Schritte zeigt die Uhr von Musti:
„15.000 werden’s locker noch bis Feierabend“.
15.000 Schritte also, das bedeutet über 10 Kilometer, zirka 300 Pakete, die aktuell pro Tag rausgehen. Bis zu 700 waren es in der Corona Hochphase. Das ist unsere Modulor Logistik in Zahlen. Heute gibt’s aber noch viel mehr als nur Zahlen: nämlich allerhand Impressionen aus dem unergründeten 2. Stock des Aufbauhauses. Dort ist nämlich aktuell noch die Logistik von Modulor angesiedelt.
Wir – das sind Pia, Philipp und Mirjam – haben unseren Kolleginnen und Kollegen im Lager mal einen Besuch abgestattet. Sind ihnen beim Kommissionieren auf Schritt und Tritt durch die Gänge gefolgt. Haben ihnen ĂĽber die Schulter geschaut, sie mit Fragen gelöchert, uns zeigen lassen, was an sämtlichen Stationen – von Wareneingang, ĂĽber Retoure und Einlagern, bis hin zum Verpacken – so passiert. Und lasst euch gesagt sein, da passiert einiges. Die Jungs und Mädels hier geben nämlich ganz schön Gas.
Was seit Corona anders ist? Wie viele Kilometer man beim Kommissionieren täglich zurücklegt? Welches Produkt bei den Verpackern am allerwenigsten beliebt ist? Was es mit den Räumen X und Y auf sich hat und wofür es einen Checker braucht? Finden wir’s raus.
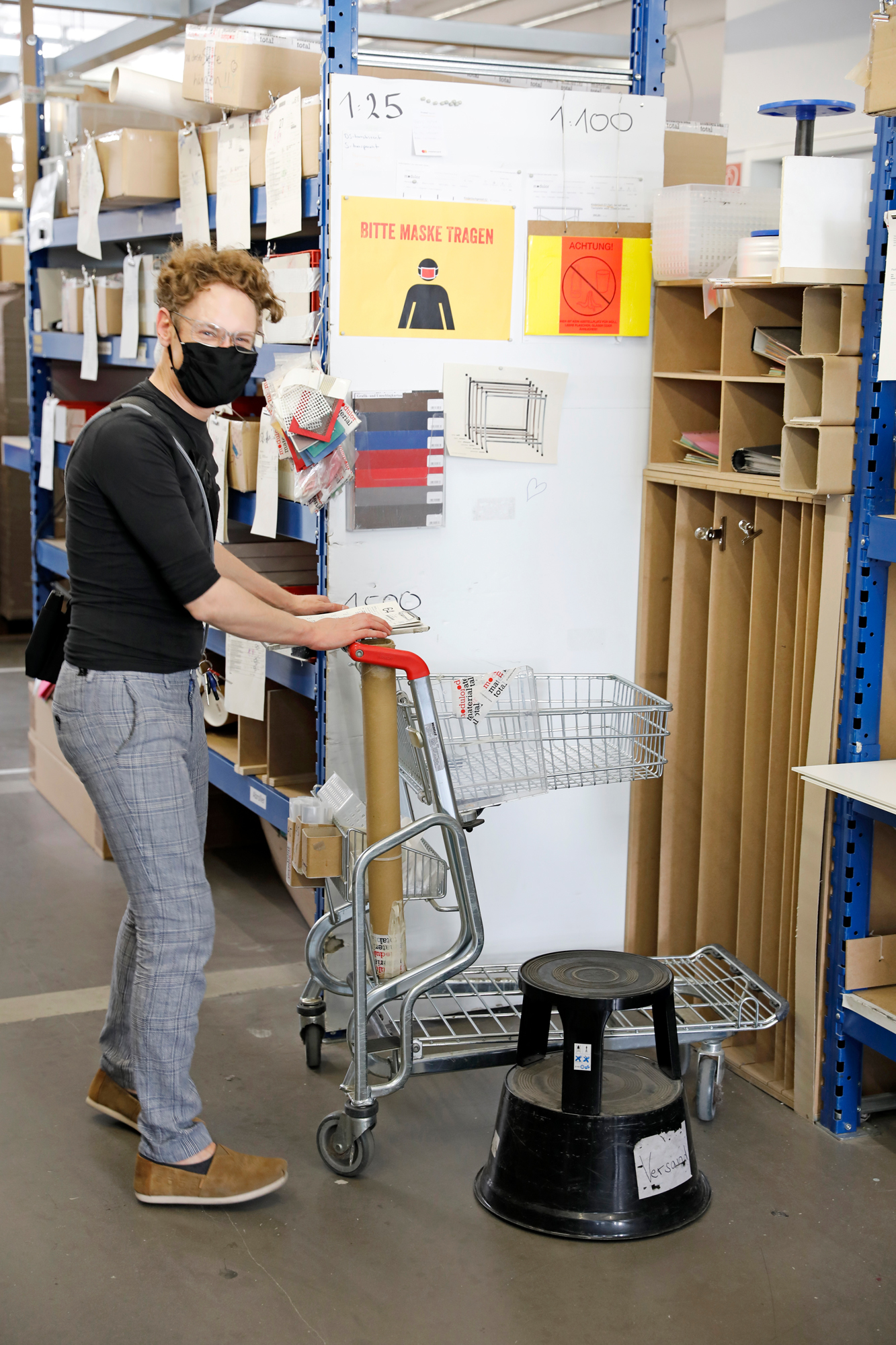

Kevin, hier beim Kommissionieren im Laden. Und zwar dermaĂźen flink, dass wir glatt Probleme hatten, ein scharfes Foto von ihm zu bekommen.
Pia: Christian, erzähl doch mal, was sind die Besonderheiten der Logistik bei Modulor?
Christian, Abteilungsleiter der Logistik:  Die Besonderheit? Wir sind ziemlich oldschool. Also die Herausforderung ist hier im Endeffekt, dass wir das alles noch analog machen. Wir erstellen Kommissionierlisten auf Papier und die Jungs und Mädels müssen damit losgehen. Sie müssen dann alles händisch abhaken und dabei ganz genau kontrollieren, ob sie auch wirklich die richtige Artikelnummer haben. Das würde normalerweise der Handscanner machen. Wenn man den anschließt und alles etikettiert wäre, würde er sagen: Halt! Falscher Artikel.
Durch das komplett analoge Arbeiten ist man natürlich fehleranfällig, weil jeder Mitarbeiter auch mal Zahlen verwechseln kann. Es liegen teilweise Artikel nebeneinander, die fast identische Nummern haben. Und nach so 6–7 Arbeitsstunden lässt dann die Konzentration auch ein bisschen nach und da kann es schon mal passieren, dass man mit einem falschen Artikel zurückkommt.
Genauso ist es mit dem Vermessen von Stäben und Rundrohren. Hier greift man schnell ins falsche Fach. Da geht es ja oft nur um einen Millimeter. Und weil diese Artikel bei uns nicht etikettiert sind, bringst Du halt mal die falsche Ware mit. Also ist es schon eine relativ komplexe Aufgabe, bei der viel vom Mitarbeiter gefordert wird, weil er halt wirklich sehr viel mitdenken muss. Bei den anderen Unternehmen sind die Sachen voretikettiert, hast du den Handscanner und er sagt: Beeep, falscher Artikel. Ist also recht monoton.
Bei Modulor ist es so: gucken, mitdenken. Habe ich das richtige nachgemessen? Selbst wenn es im richtigen Fach liegt und richtig bezeichnet ist, sagen wir trotzdem: Hey, immer wieder nachmessen ob es wirklich dieser Artikel ist.
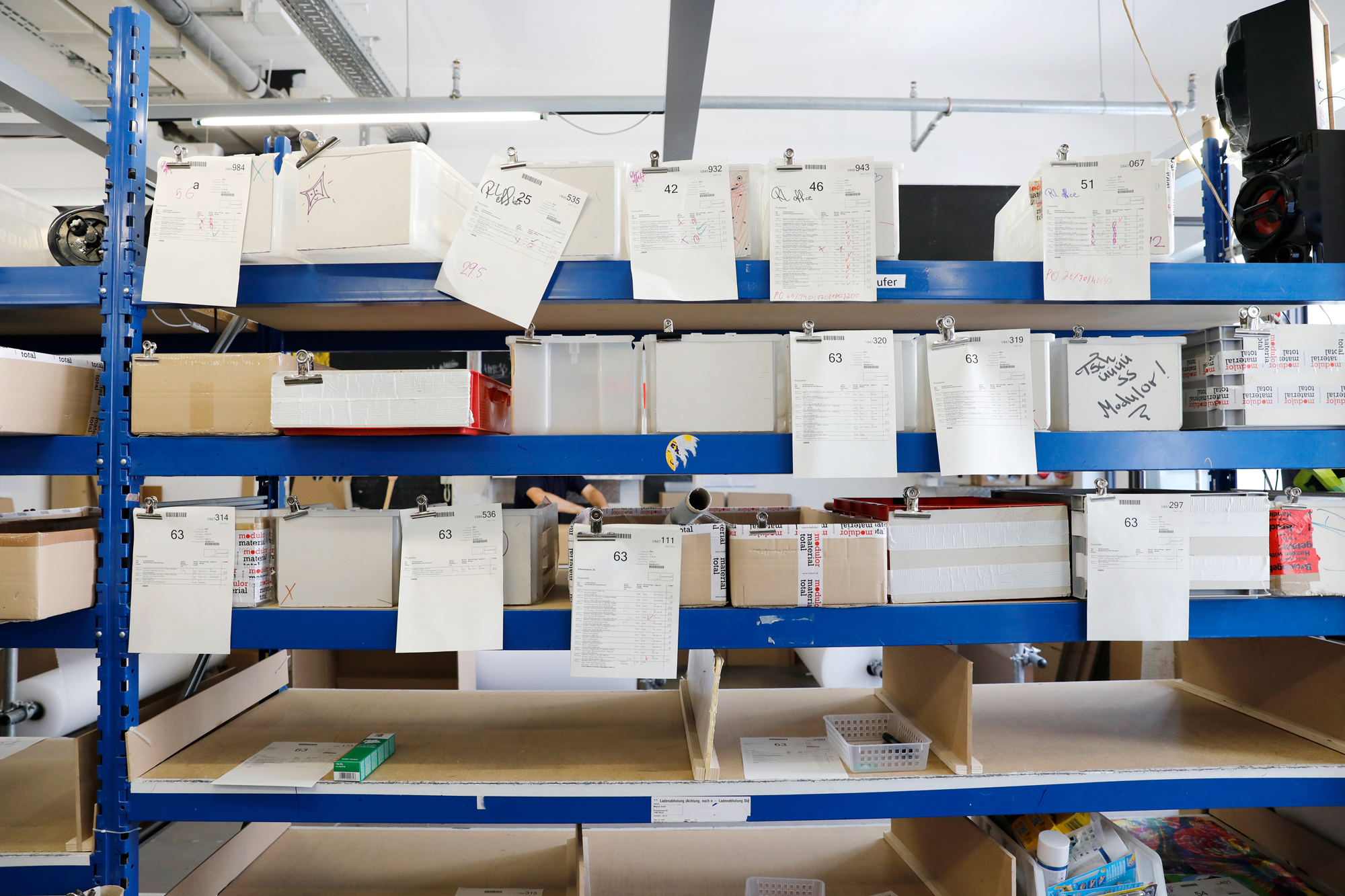
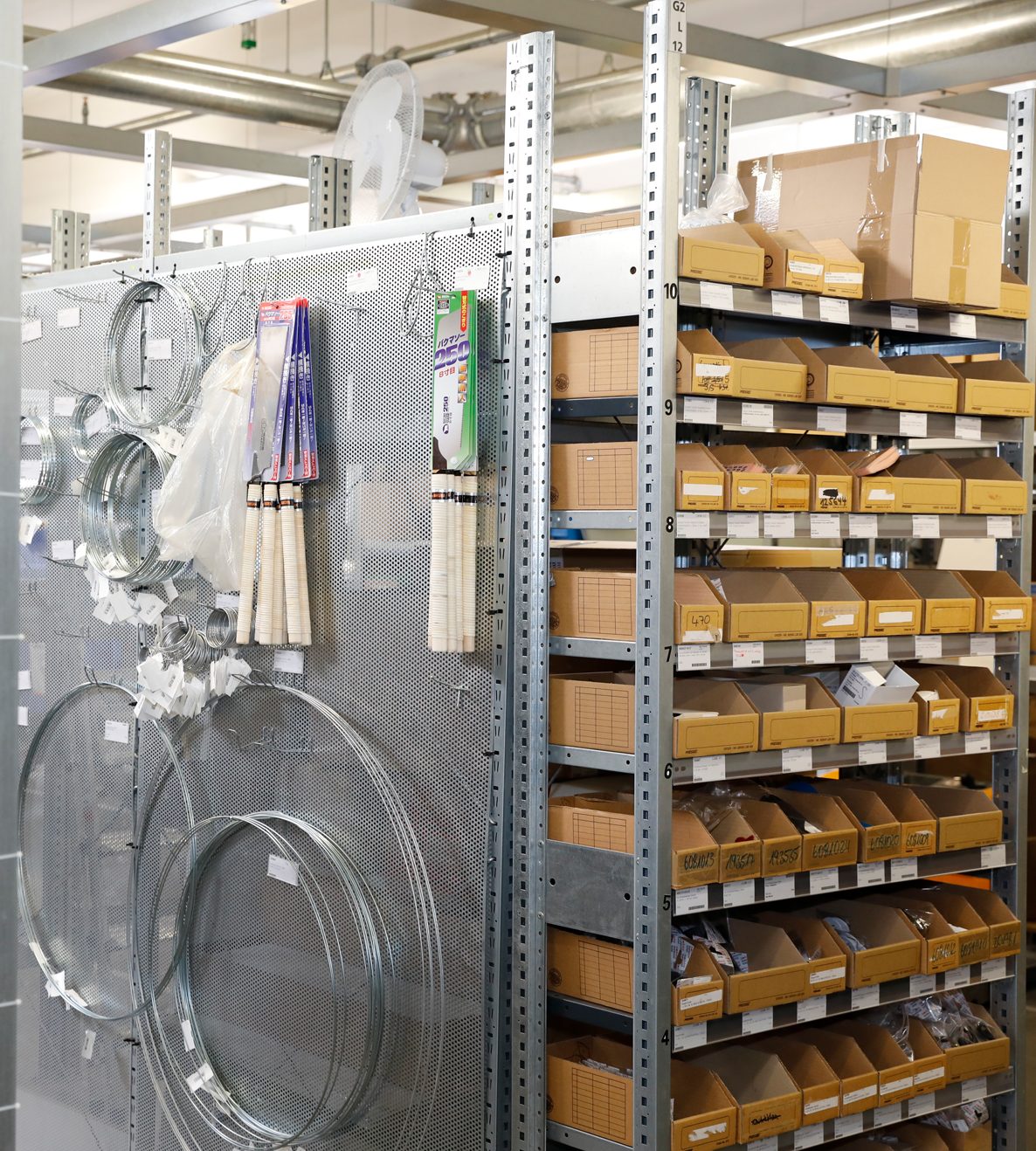
Aber bevor die Bestellung rausgeht, werden die Produkte nochmal gecheckt, richtig?
Christian: Genau, hierfür gibt es die Checker. Es ist quasi ein Vier-Augen-Prinzip. Jeder, der kommissioniert, kann Fehler machen. Er oder sie ist ja auch nur ein Mensch. Jeder hier kennt zwar unsere Materialien und Produkte, aber Fehler passieren trotzdem. Deshalb wird nochmals geprüft: Ist der Auftrag vollzählig und ist denn auch das Richtige drin?
Und sollte das nicht der Fall sein, ist es einfach so: Der Mitarbeiter muss sein KĂĽrzel hinterlassen. Also weiĂź man, welches Material er oder sie geholt hat. Meistens wird dann auch genau diese Person nochmal losgeschickt, um das richtige zu holen. Einfach damit man aus dem Fehler lernt: :„Ah Ok, pass auf, ich habe genau das und das falsch gemacht“.Â
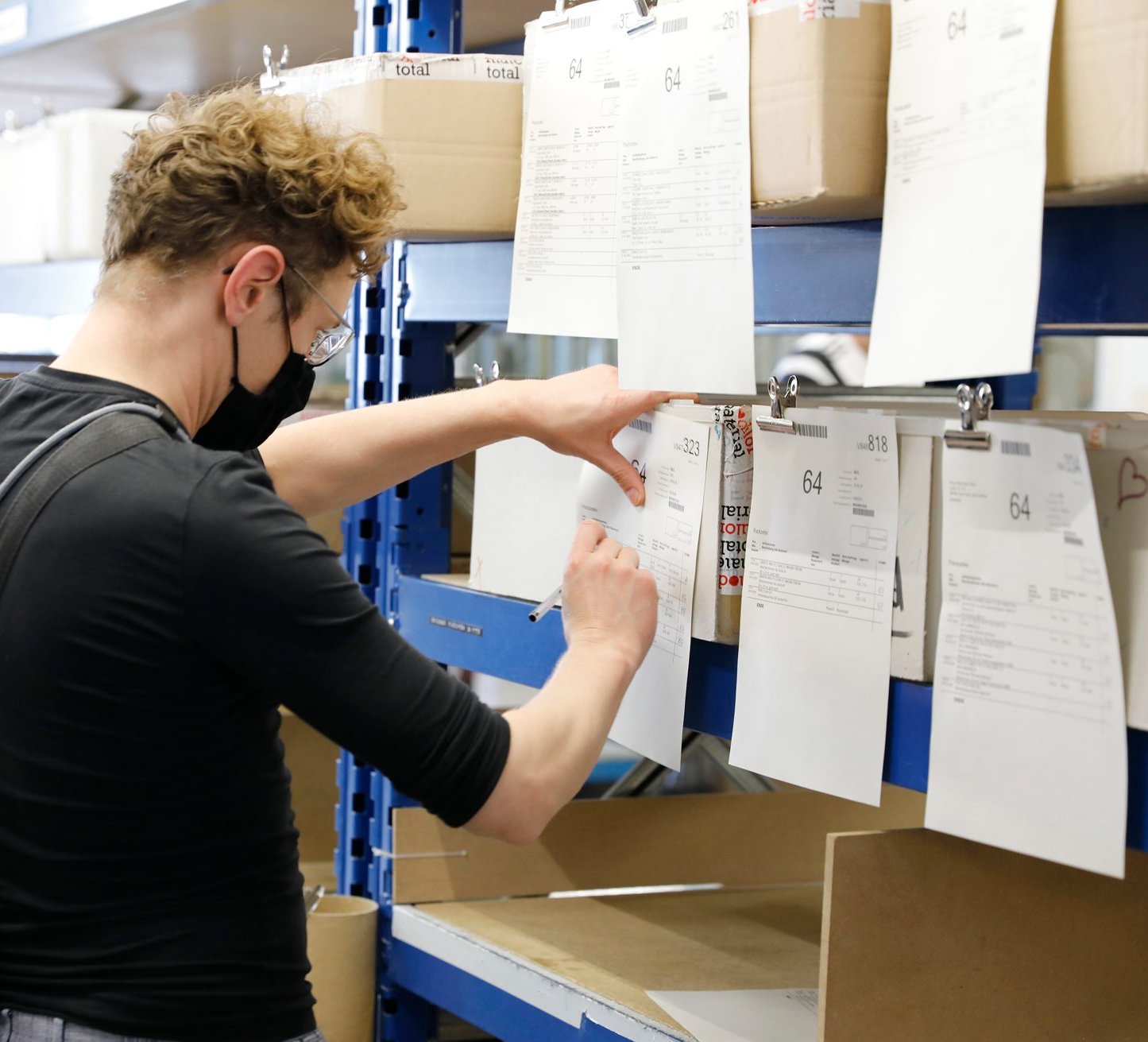
Was hat es mit den Papphalterungen an den Kommissionierwägen auf sich? Das sieht nach einer modulorigen Lösung fĂĽr ein Problem aus…
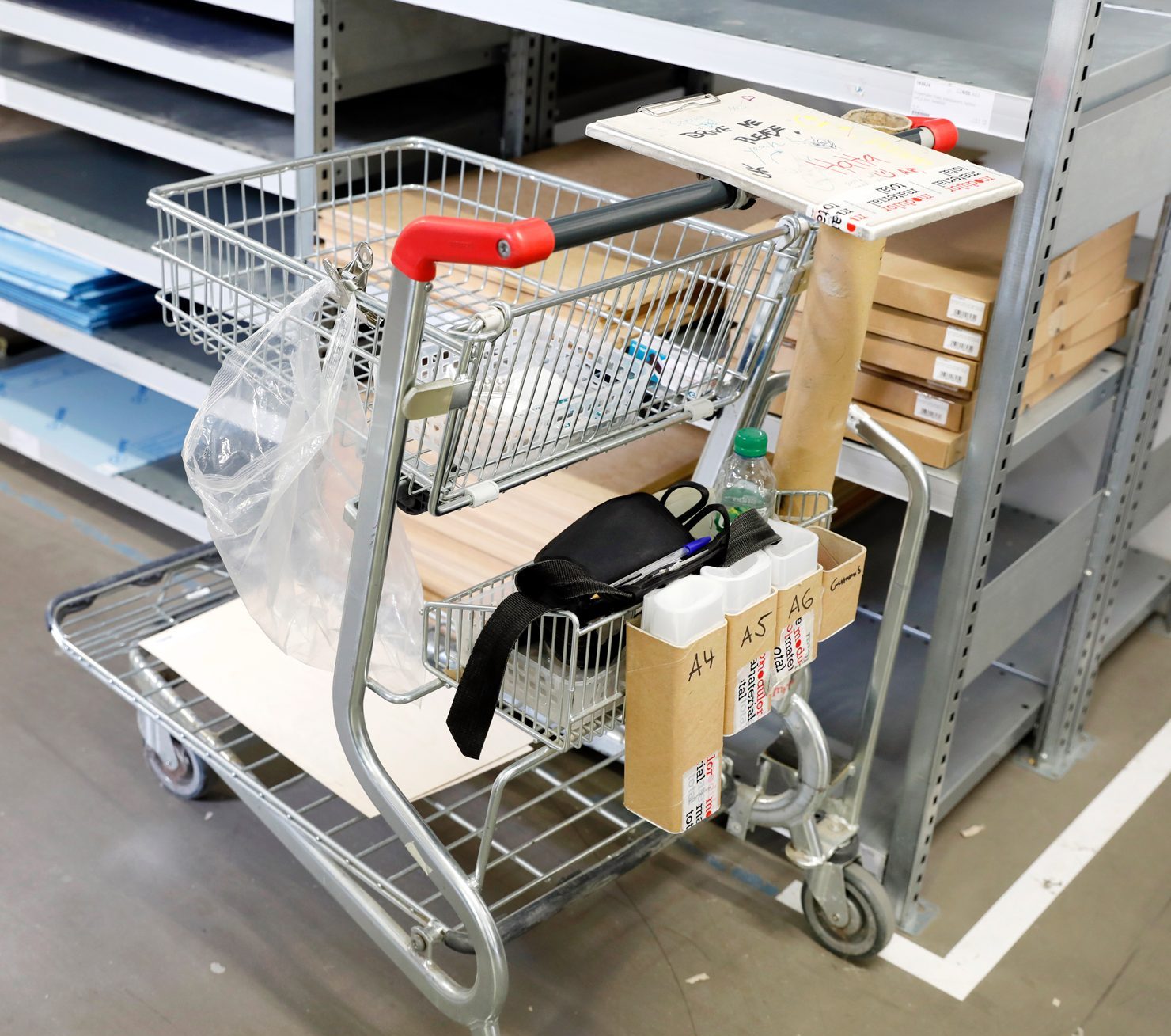
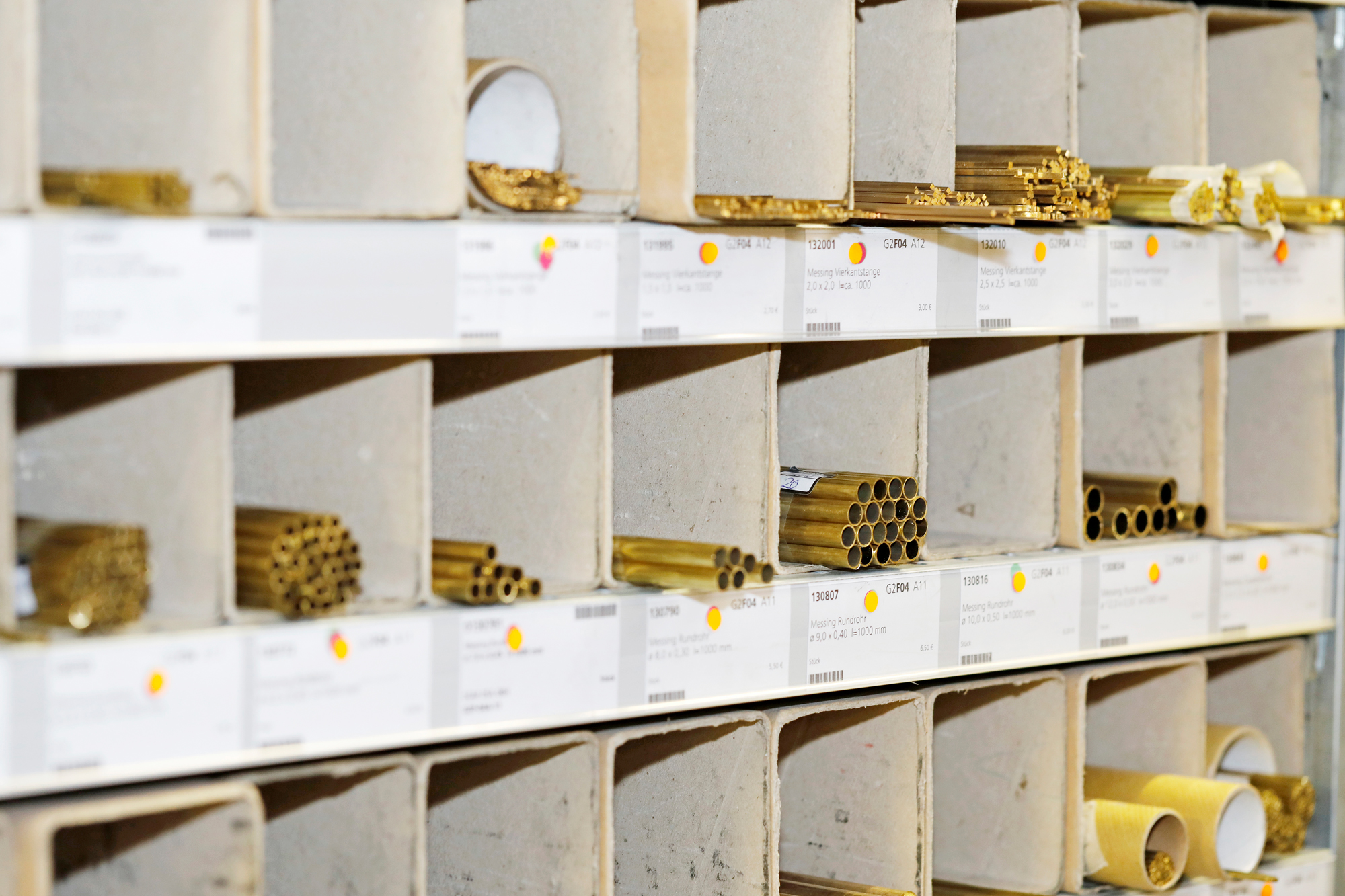
Christian: Ja, das ist aus der Frage entstanden, wie wir bestimmte Materialien am besten transportiert bekommen. Die Rundrohre an den Wägen sind da, damit diese kleinen Holzstäbchen, die sehr fein und dünn sind, nicht einfach so im Wagen liegen. Du legst ja andere Ware drauf, da würden die sonst schnell kaputt gehen. Oder Du müsstest andauernd neu umstrukturieren. „Jetzt nehme ich die Stäbchen nochmal raus, damit ich die Papiere reinlegen kann“. So hast Du für bestimmte Produkte eben spezielle Ablagefächer. Das hilft den Kommissionierern und spart Zeit.
So, alle Teile der Bestellung sind nun kommissioniert. Und vom Checker kontrolliert. Nächster Schritt: Ganz genau, es geht ans Verpacken.Â
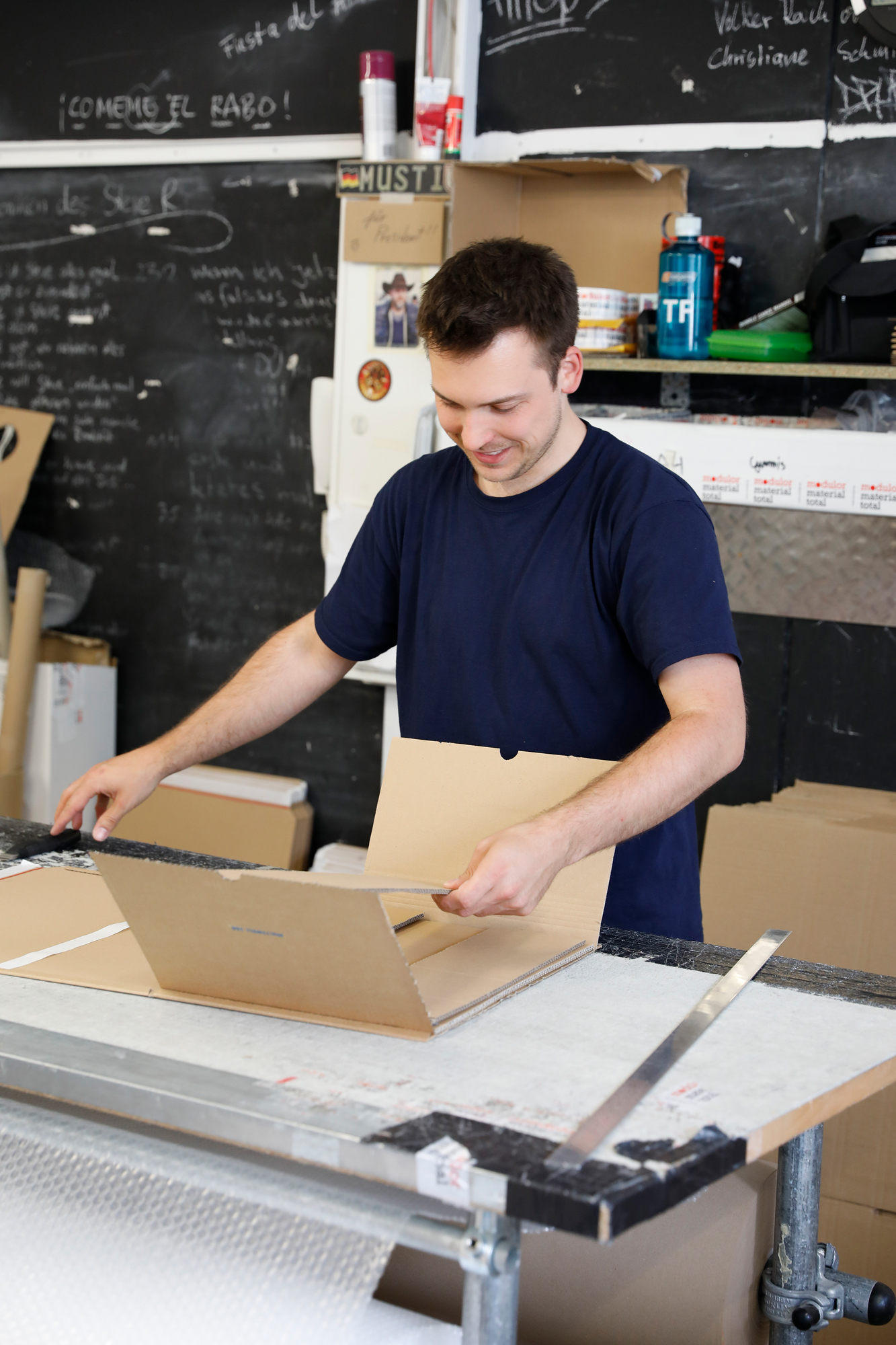
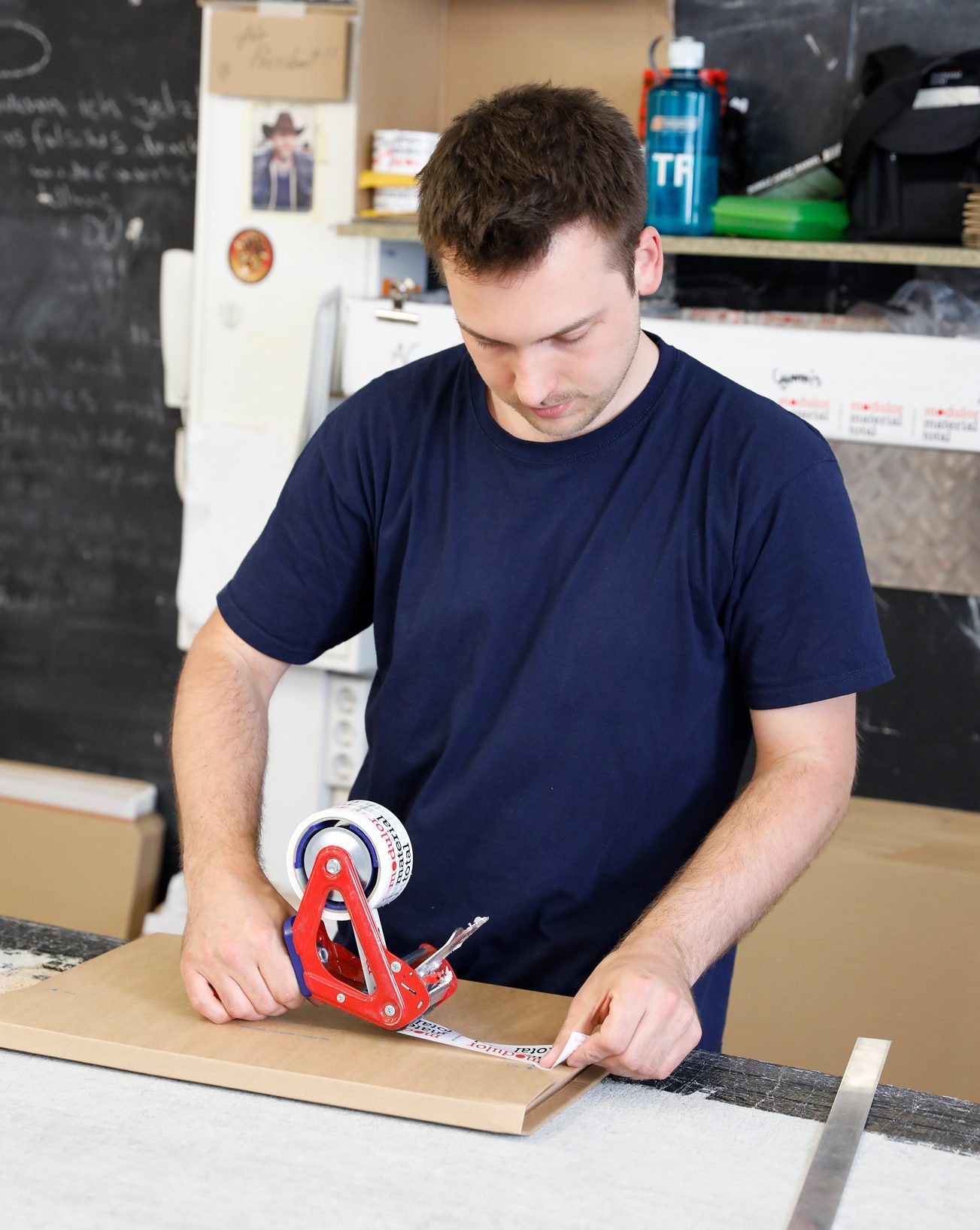
„Am liebsten sind mir die Bestellungen mit vielen Produkten in unterschiedlichen Formaten. Stäbe, Platten, Rohre… Das Ganze muss man dann irgendwie sinnvoll zusammenbasteln. Und so beim Verpacken ein bisschen erfinderisch sein.“
TimÂ
Pia: Und welches Produkt ist am allerschlimmsten zu verpacken?
Tim: Uh, ich glaube Buchbinderpappe. Die ist sau schwer. Und meistens bestellen die Kunden hier direkt 10 Stück oder mehr. Das geht beim Verpacken ganz schön auf den Rücken.
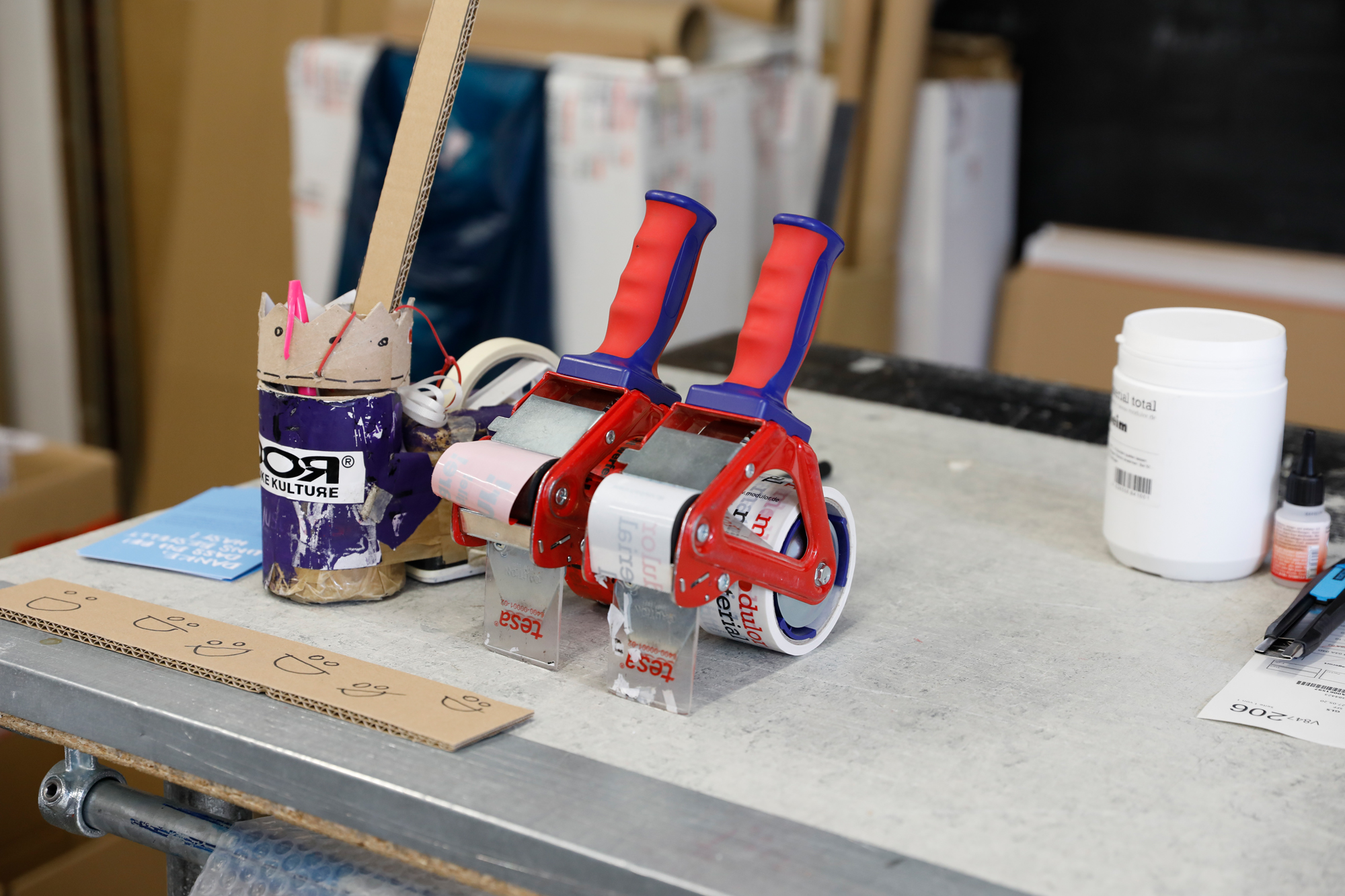
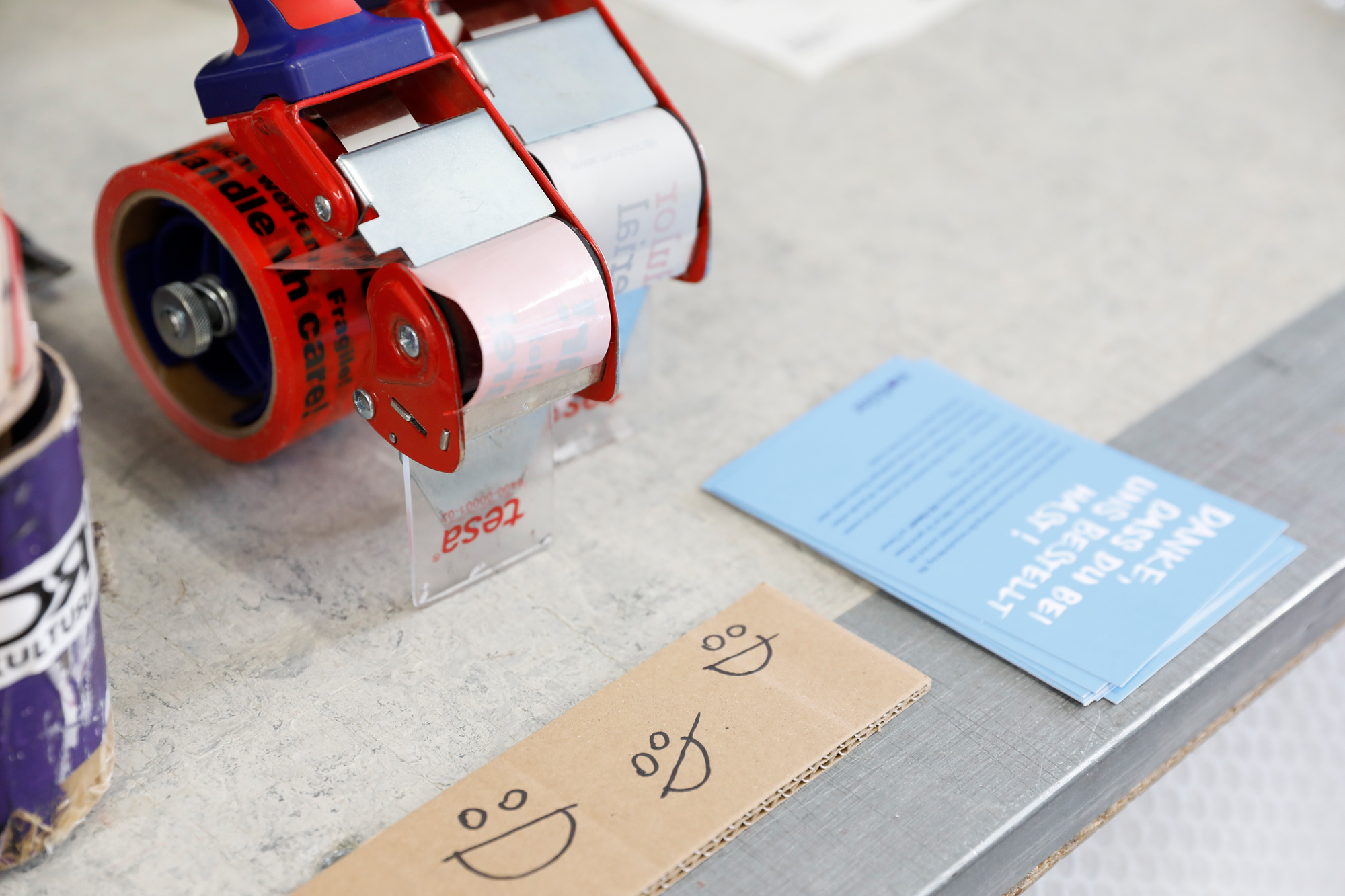

Für alle, die aktuell bestellen, gibts eine Dankeschön Karte. Die wird handsigniert. Dickes Danke für euren Support in dieser Zeit!
Wie hat sich euer Arbeiten durch Corona verändert?
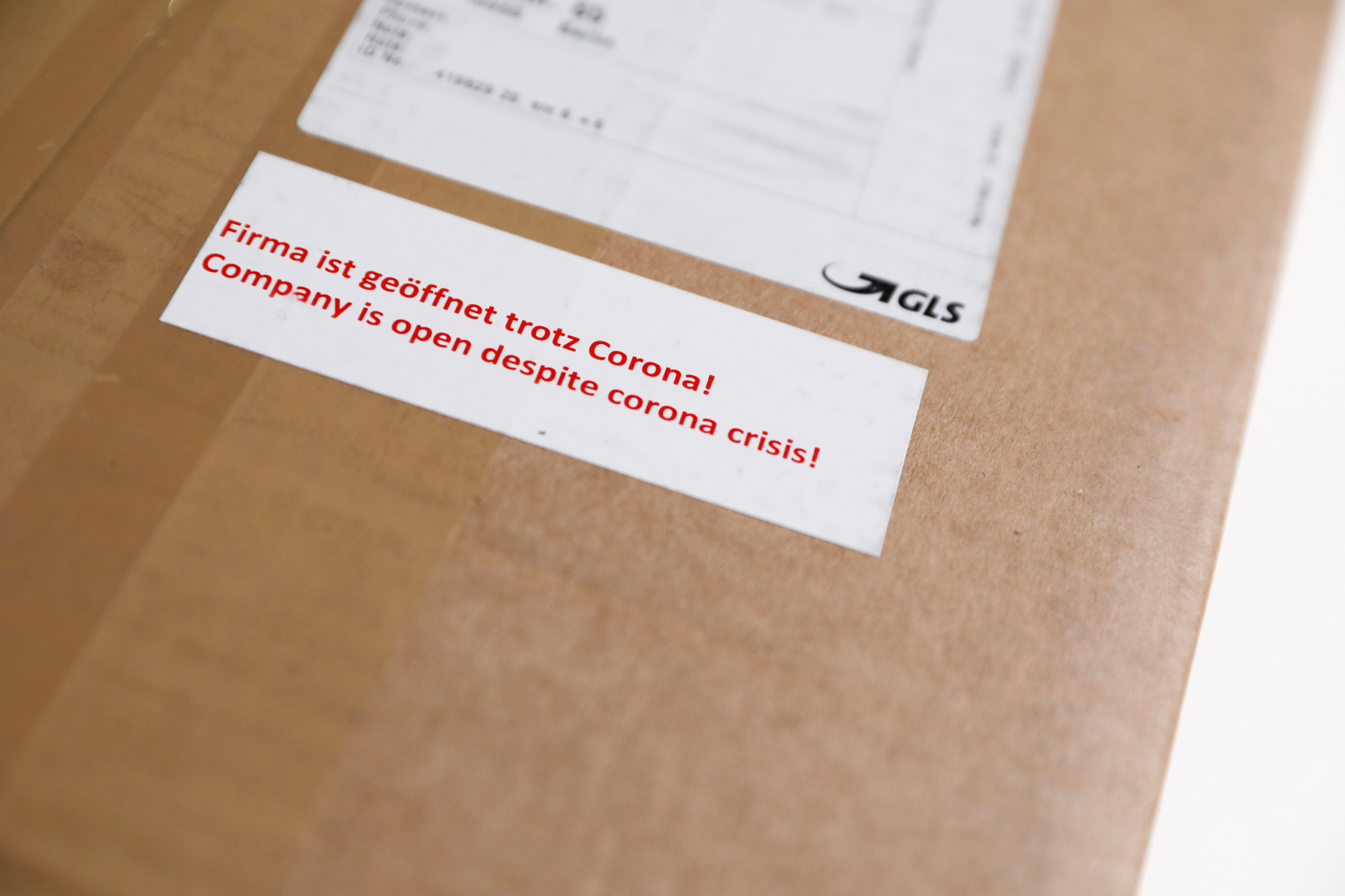
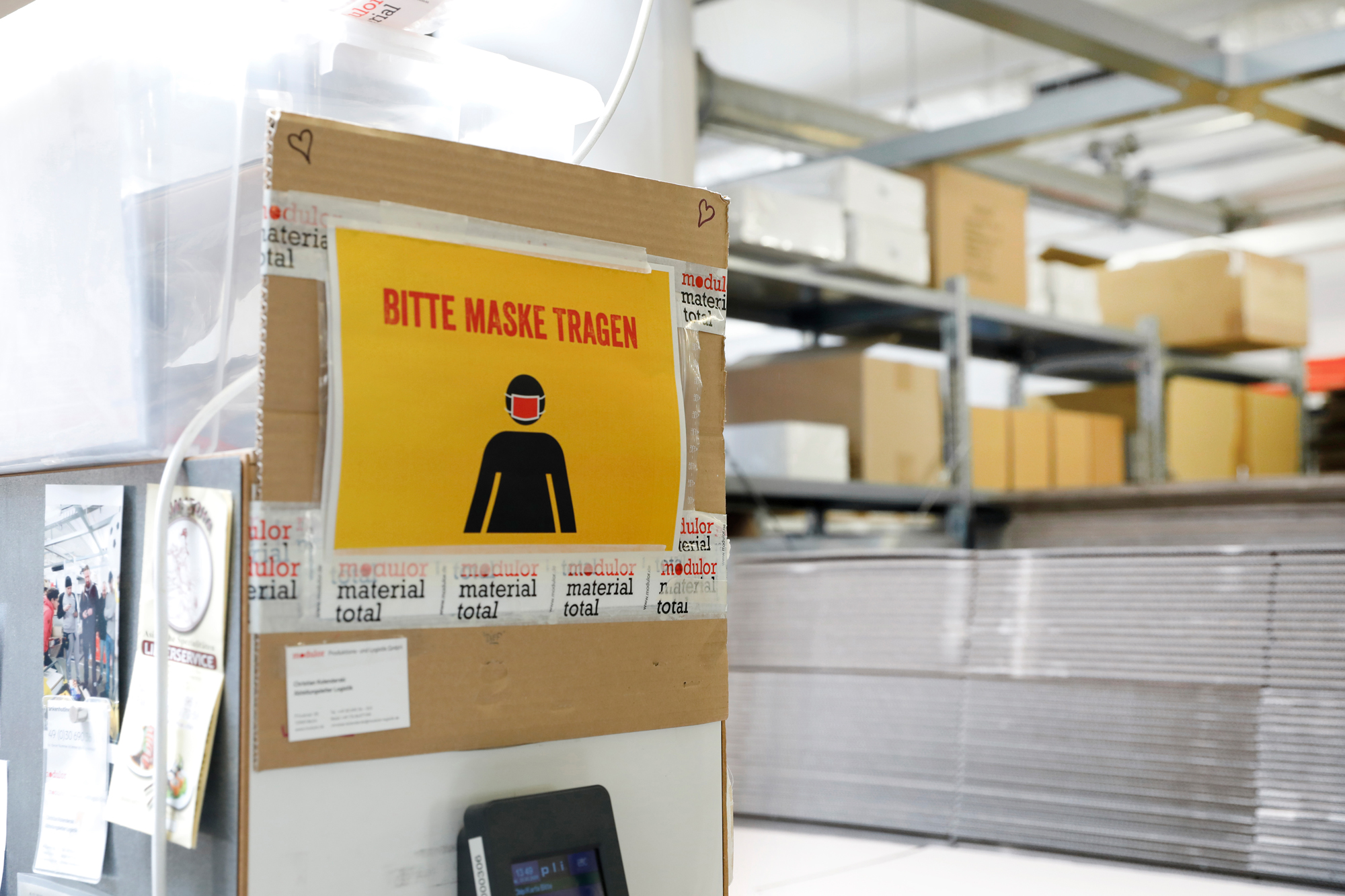
Christian:Â Gerade am Anfang kamen ja stĂĽndlich irgendwelche Meldungen raus, auf die wir reagieren mussten. Wir haben uns natĂĽrlich an die gesetzlichen Vorgaben gehalten und zum Beispiel ein Zwei-Schicht-System eingefĂĽhrt. Zwischen den Schichten gab es immer immer eine halbe Stunde Pause, damit sich jeder in Ruhe umziehen kann. Die einen gehen, die anderen kommen, ohne sich dabei zu begegnen.
Das war wichtig, damit die Logistik nicht komplett ins Stocken gerät. Und damit im Ernstfall, also wenn eine Person Corona hat, eben nur ein Team ausfällt und nicht gleich die ganze Logistik, weil alle zusammengearbeitet haben. Für uns war wichtig, dass wir sagen können: Egal wie der Zustand ist, erst einmal wir können die Logistik aufrechterhalten und auch entsprechend weiterarbeiten. Das Volumen an Aufträgen in der Zeit war schließlich fast das Dreifache von dem, was wir sonst hatten. Gerade in dieser Phase wollten und mussten wir unser Lieferversprechen einhalten und sicherstellen können, dass jeder Kunde auch bekommt, was er bei uns bestellt hat.
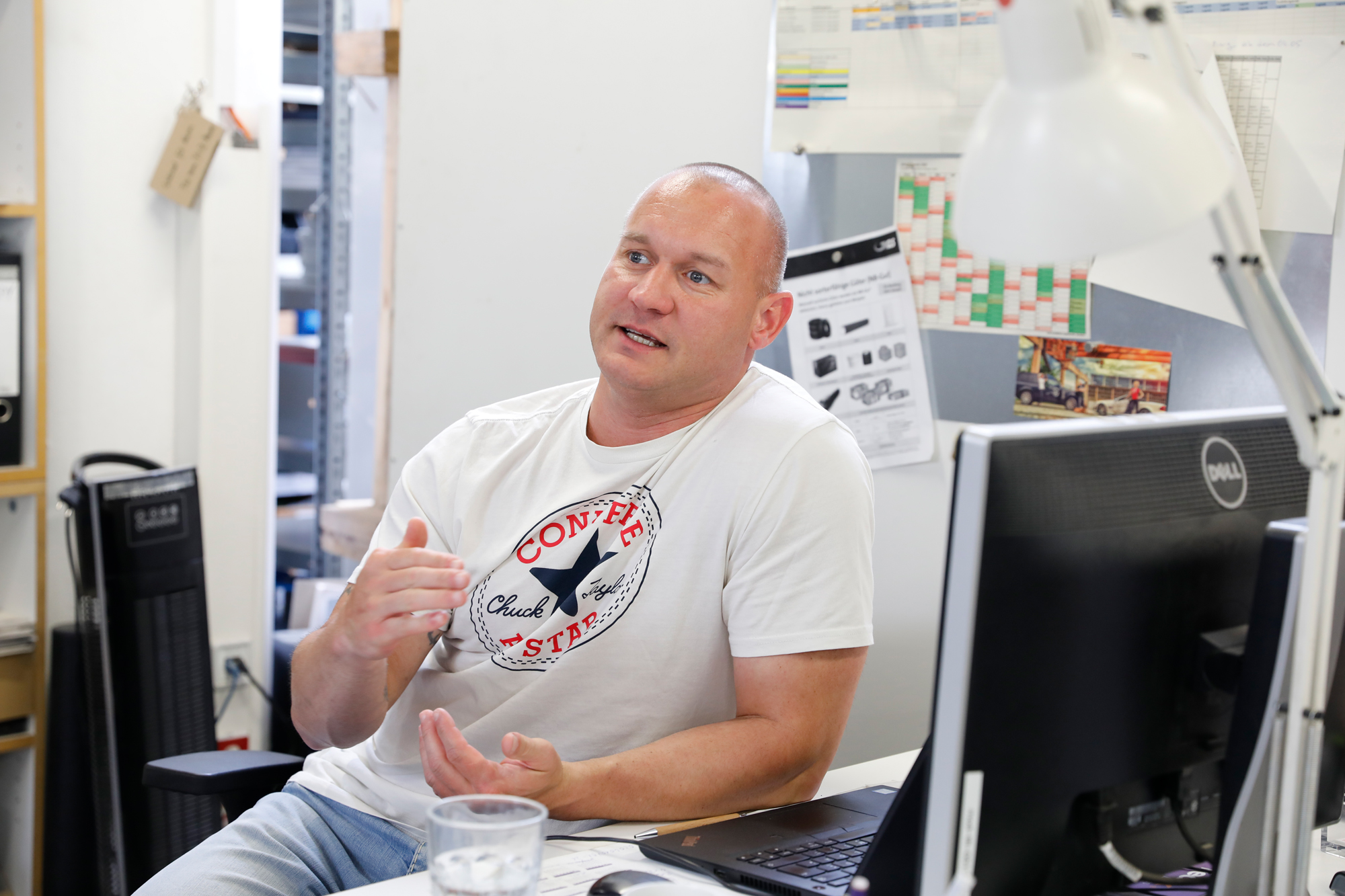
Christian, Abteilungsleiter der Logistik
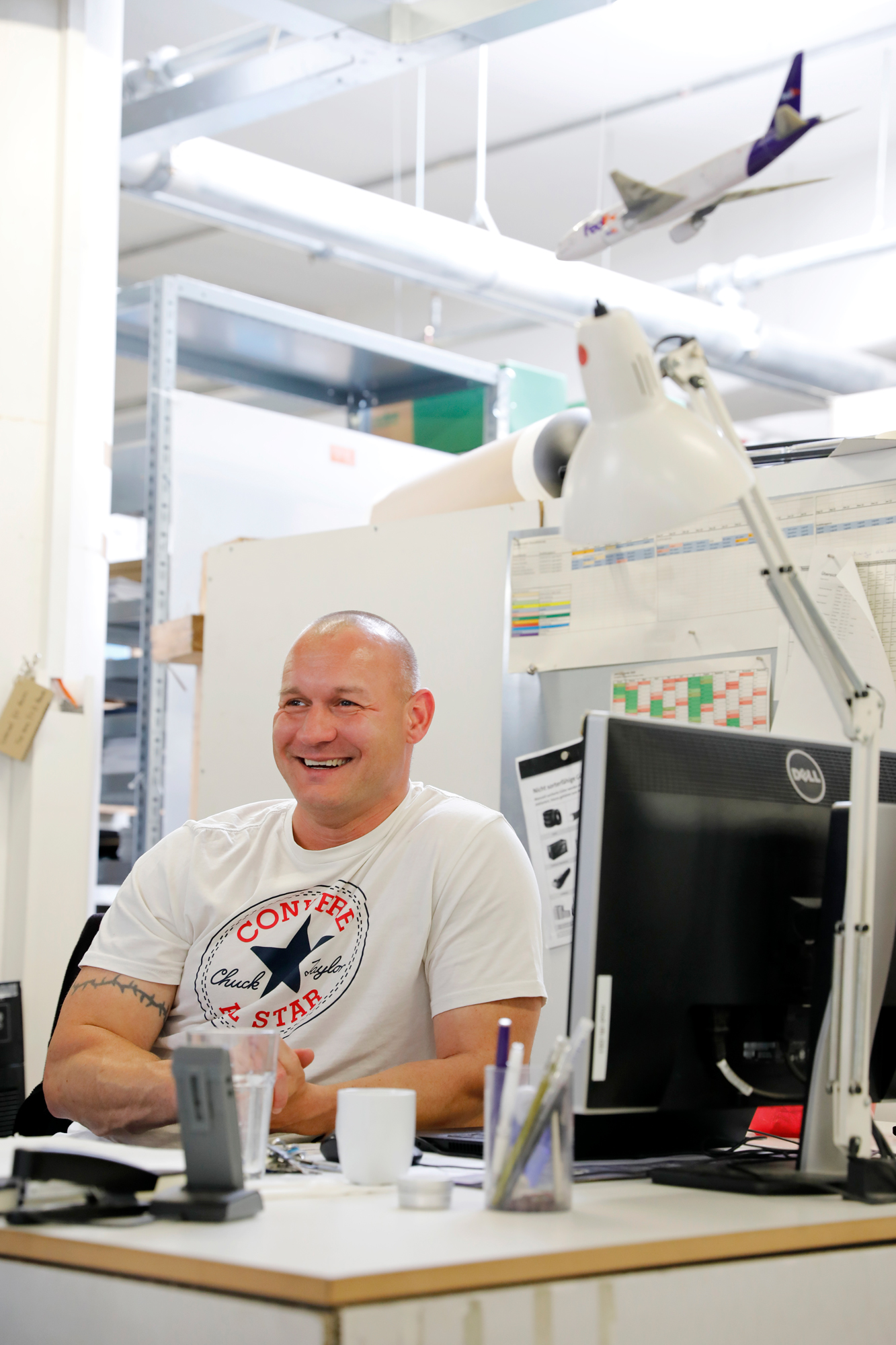
Pia: Wie viele Pakete schickt ihr hier am Tag raus? Der Laden hatte ja lange zu, wie hat sich das ausgewirkt?Â
Christian: An den Spitzentagen, wo wir im 2-Schicht-System gearbeitet haben, sind 700–750 Pakete pro Tag rausgegangen. Aktuell sind wir wieder bei so 280–320. Vor Corona waren wir vielleicht bei 200–250. Also da sieht man ganz klar, wie die Zahlen hoch gingen.
Vor Corona gab es bei den Bestellungen immer Montags, Dienstags, Mittwochs ein Peak. Jetzt hält sich immer noch ein erhöhtes, aber auch mit einem Team schaffbares Volumen über die ganze Woche. Das Gute ist, dass wir auch einen relativ guten Spediteur haben und wir die Pakete wirklich innerhalb von 2–3 Tagen ausgeliefert bekommen.
So das Paket ist also verpackt und bereit zum Verschicken. Aber Moment mal, wir haben da doch was ausgelassen. Und zwar den Wareneingang.
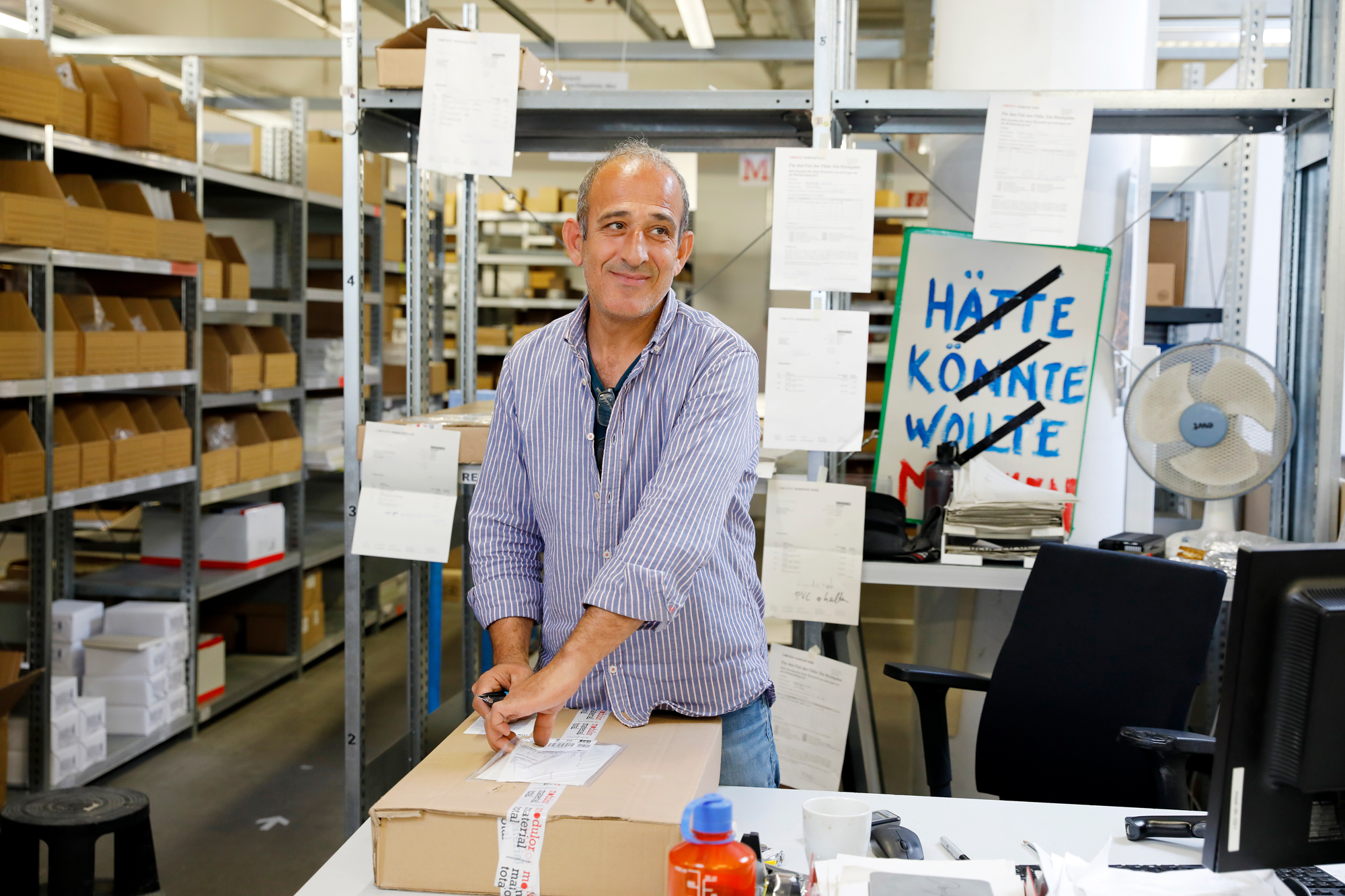
„Montageumlagerung, Außenlagerumlagerung, Zuverdienst, Retouren, normale Waren annehmen… viel passiert hier.
Da müsst ich 2–3 Bier trinken, dann könnte ich euch stundenlang darüber erzählen. “Yusuf
Philipp: Yusuf, Du schaust schon so…
Yusuf: Schau Dir mal den Wareneingang hier an. Weil wir vor ein, zwei Wochen wieder anfangen konnten Ware zu bestellen, kommen gerade gefühlt 20–30 Paletten jeden Tag an. Das ist viel. Was wir normal in einem Monat bekommen, kriegen wir jetzt innerhalb von zwei Tagen. Deswegen sieht es hier so wild aus.
Und was passiert jetzt damit?
Yusuf: Wir müssen die Ware erst einmal einlagern. Und dann gibt es die Umlagerung. Einiges geht direkt ins EG, also in den Laden. Heute Nacht wird automatisch eine Liste erstellt: Das wurde heute verkauft, das soll automatisch runter gehen. Man muss ja die Bestände wieder auffüllen. Wir kommissionieren dann die Produkte und bringen alles nach unten. Und die Ladenleute lagern das entsprechend ein. Damit die Regale voll sind, sobald die Leute in den Laden kommen.
„Umso schneller wir jetzt im Wareneingang arbeiten, und die Ware wieder in die Regale rein bekommen, desto besser ist das für uns alle und am Ende auch für den Kunden, damit der auch die Ware bei uns bekommt, die er braucht.“
Christian
Pia: Wow, und wie viele seid ihr hier?
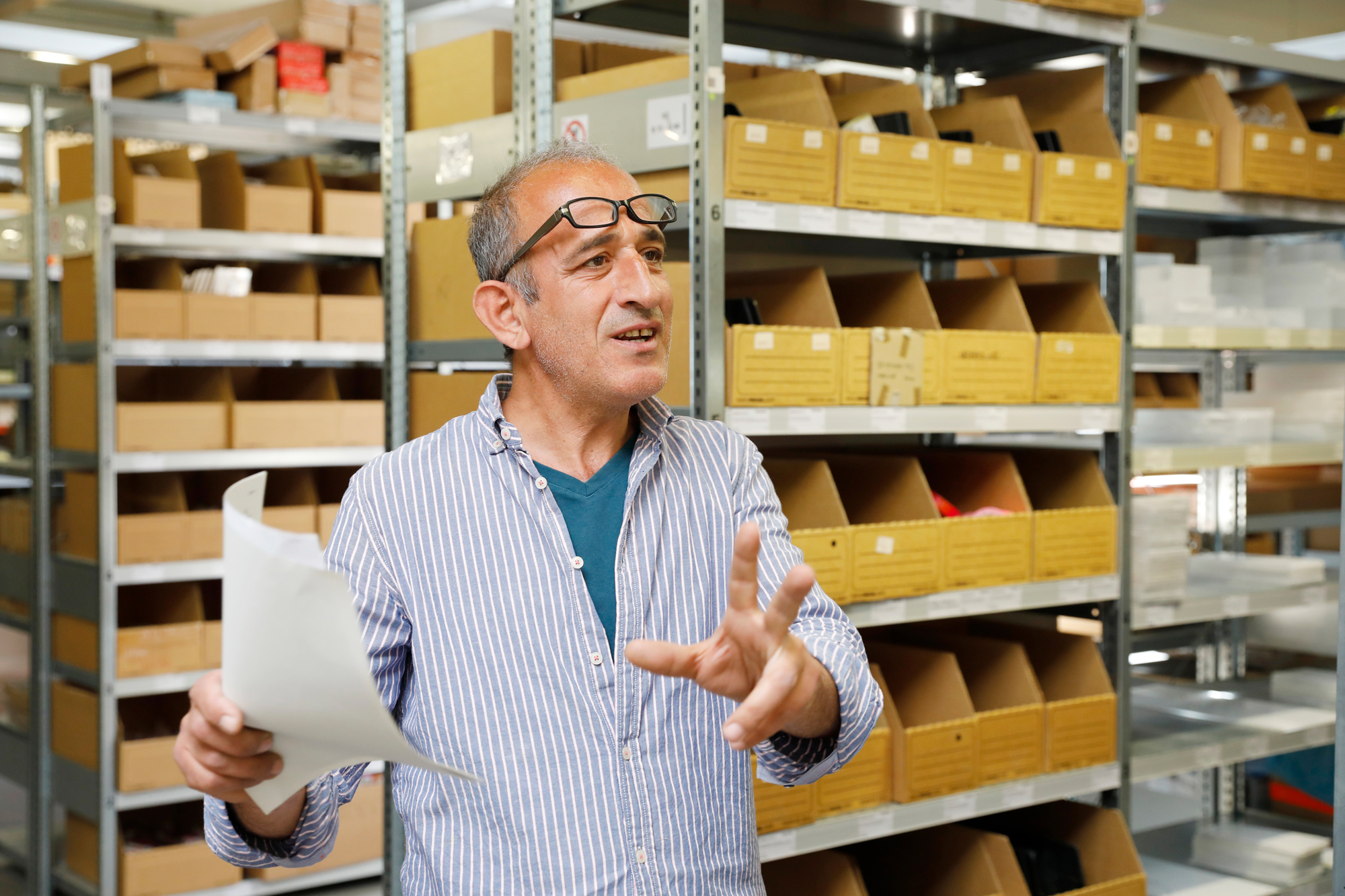
Yusuf: Hier im Wareneingang arbeiten 15 Leute. Mit Azubis. Wisst ihr, der Wareneingang muss Frühschicht bis Spätschicht haben, weil der Laden bis 20 Uhr auf ist.
Wir fangen hier um 7 Uhr normalerweise an. Bis 20 Uhr muss immer jemand hier sein. Weil eben jemand aus dem Laden anruft fĂĽr eine Sofortumlagerung.
Der Kunde kommt, er braucht 10 Holzkugeln, wir haben nur fĂĽnf unten. Dann kommt der Anruf: „Hallo der Kunde ist da, könnt ihr uns das und das runterschicken!“. Das muss dann sofort passieren. Es gibt also Spätschicht, FrĂĽhschicht und eine Samstagsschicht.
Ab nächster Woche kommen noch weitere Azubis. Die sind aber nicht alle für die Logisitk, sondern auch für den Laden, also Einzelhändler, oder auch für das Büro drüben. Aber alle fangen hier an, damit sie die Ware kennenlernen und die Prozesse verstehen.
Das wird gemacht, damit derjenige wirklich sieht: Was passiert hier? Die Ware kommt rein, schön und gut, aber wie und was passiert weiter? Wie wird das für den Laden vorbereitet? Wie wird kommissioniert? Das machen wir bei jedem Mitarbeiter, der bei Modulor beginnt.
Alles beginnt in der Logistik.Â
Dem ist wohl nichts mehr hinzuzufügen. Außer: Ein dickes fettes Danke an all unsere Kollegen aus der Logsitik! Danke, dass ihr euch Zeit genommen habt für uns. Danke, dass wir euch von der Arbeit abhalten und im Weg rumstehen durften. Und vor allem: Danke für das, was ihr in den letzten Wochen geleistet habt. Ihr seid spitze! 👏
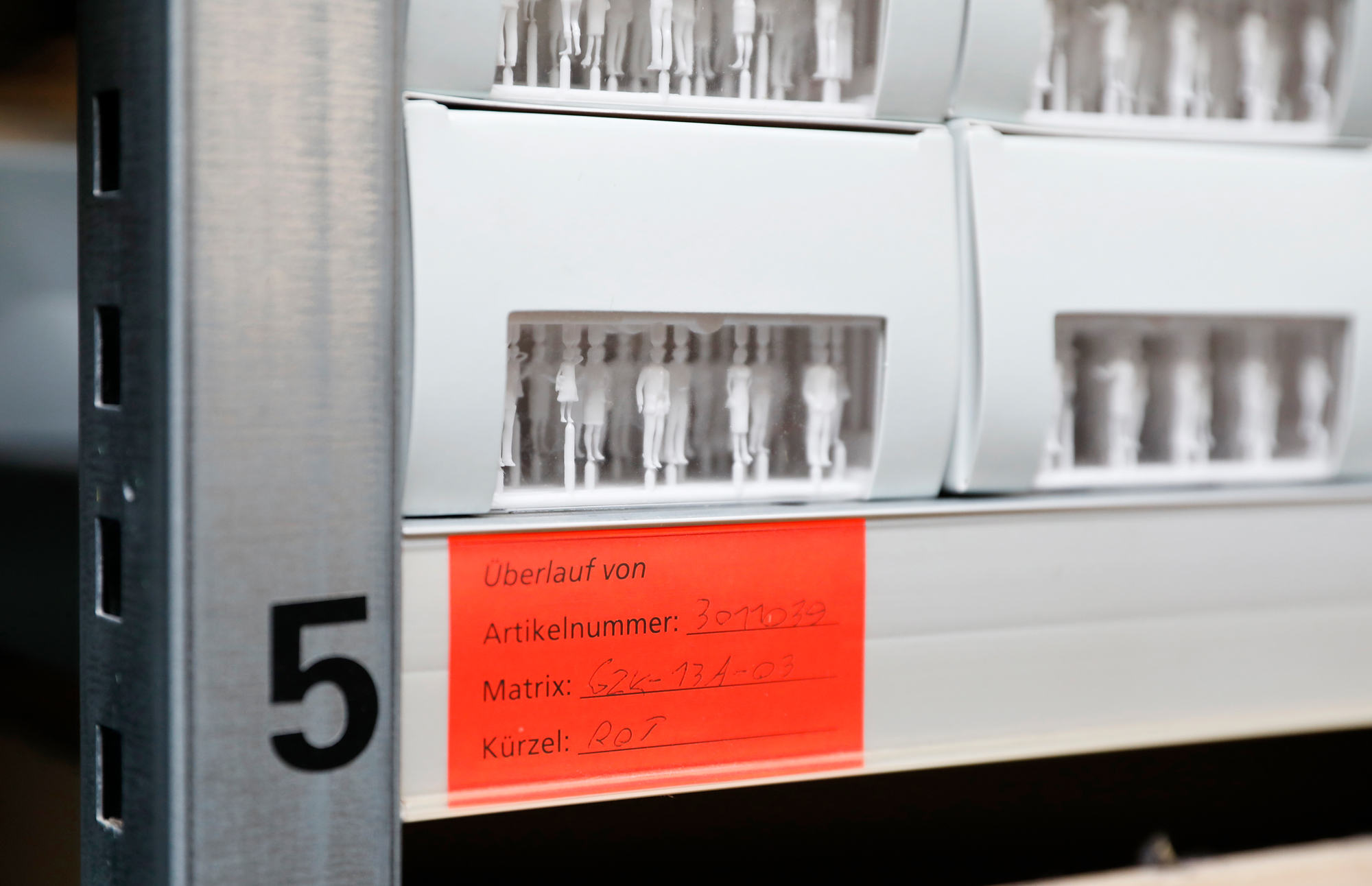
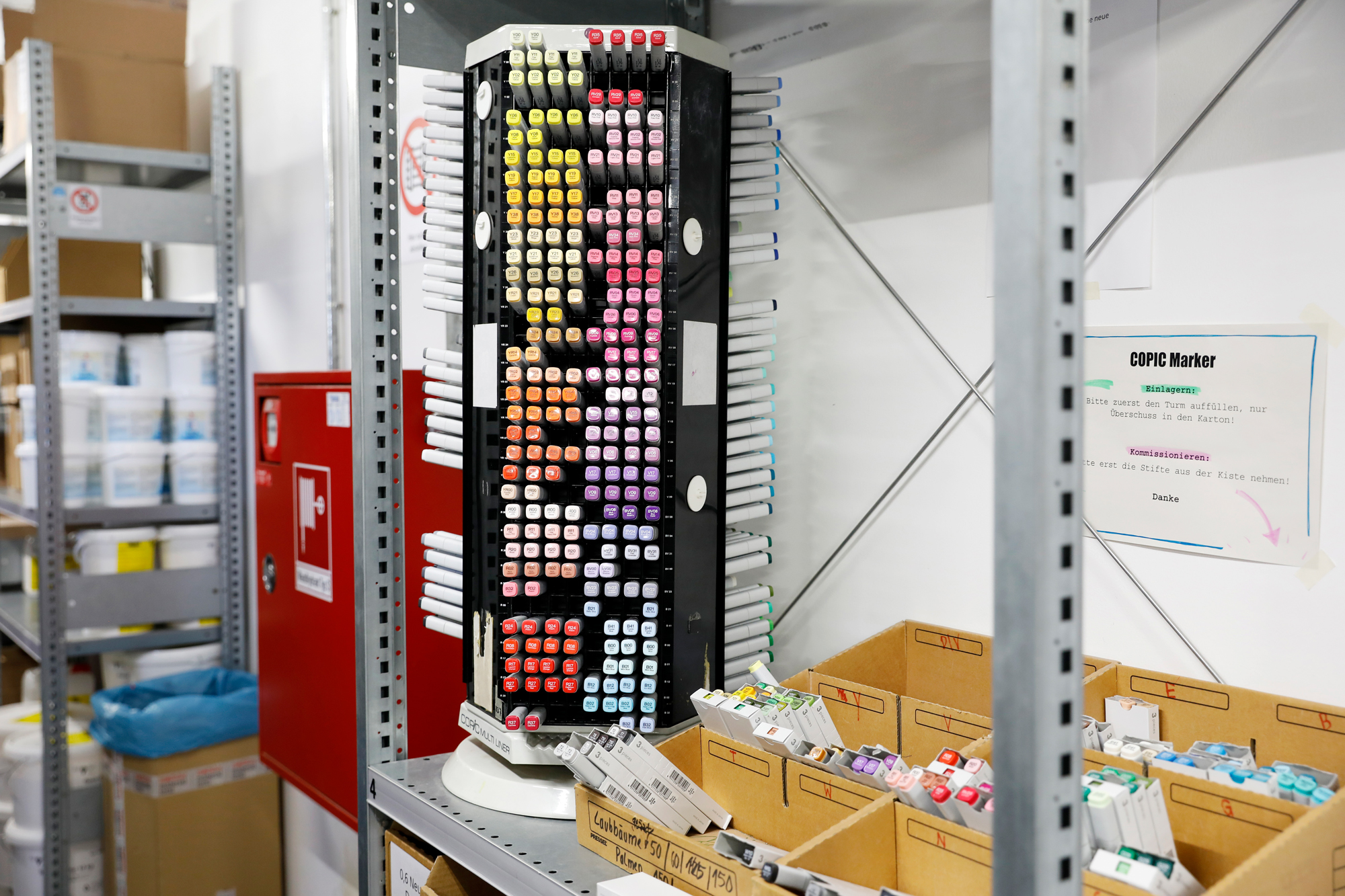
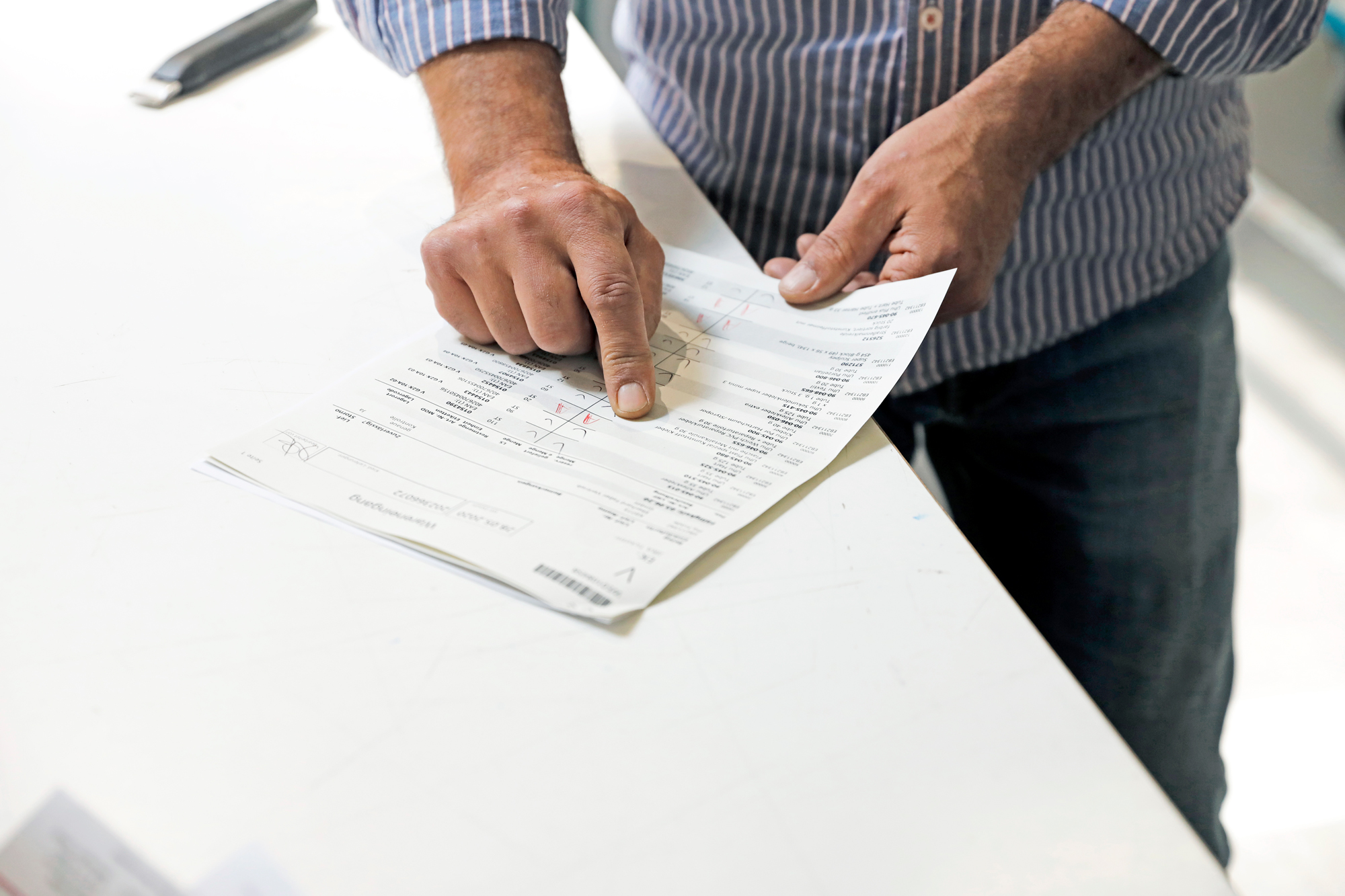
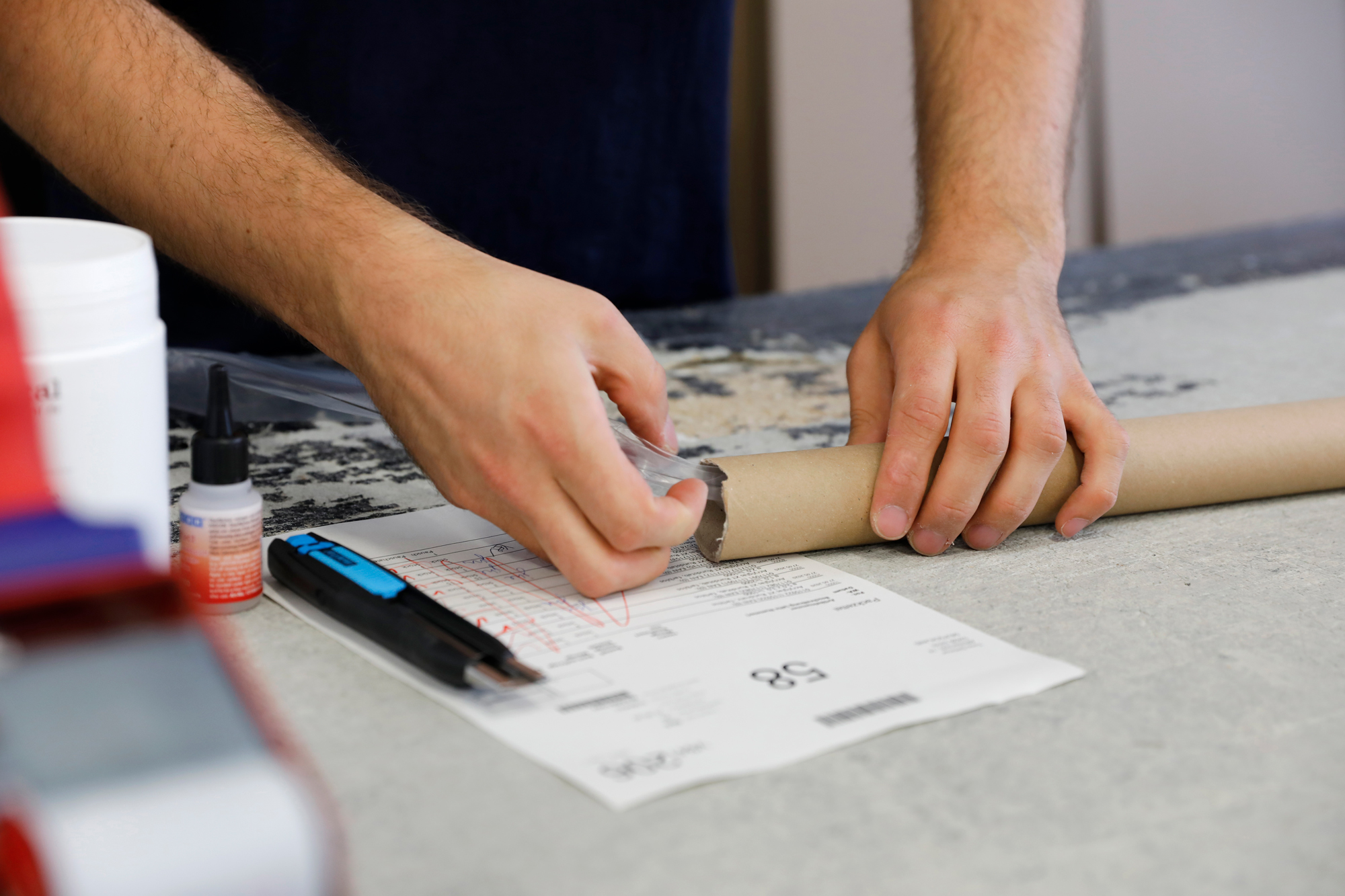
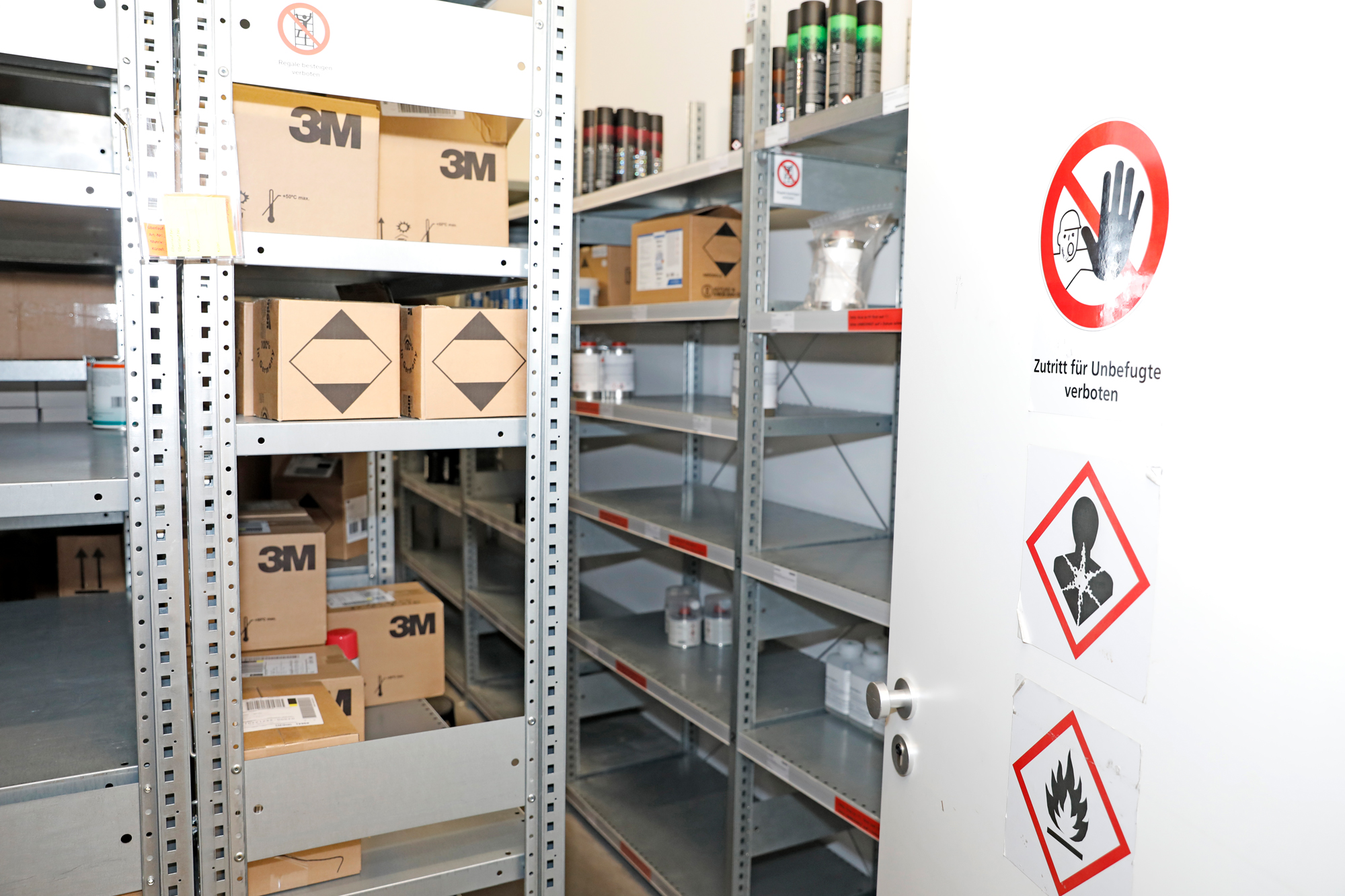